A Spa is a place where you can relax and take care of yourself. They offer all kinds of treatments to improve your well-being. It can also help to prevent diseases.
High-tech tools, such as LED, microcurrent and cryotherapy are on the rise in the spa industry. These devices will help spas to diagnose skin and health problems more accurately and create a personalized experience for their clients. Click the https://spakingsaz.com/ to learn more.
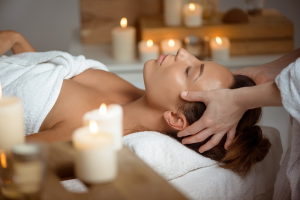
Stress relaxation is a way to help reduce the effects of daily life by slowing down the body and quieting the mind. This can be done through a variety of techniques, such as meditation, deep breathing exercises, visual imagery, and other mindfulness practices. Many people find that these methods are effective in lowering their levels of stress, though they can take time to work and may require regular practice over long periods of time. Some may need the assistance of a counselor or mental health professional to learn how to incorporate these techniques into their routines.
Spas are places where you can indulge your body and senses with relaxing treatments. They have been popular since ancient times, when Romans and Greeks would soak in natural thermal mineral springs to soothe sore muscles and rejuvenate their bodies. Today, spas offer a wide variety of treatment options, from boosting immunity in subzero cryotherapy chambers to exfoliating your skin with red wine ’vinotherapy’ scrubs. The term “spa” can also refer to a massage salon, where you can get a relaxing, therapeutic massage or even a facial that leaves your skin glowing.
Relaxation can be beneficial for everyone, no matter your age or medical conditions. It can improve your physical well-being, boost your energy, and help you deal with the challenges of everyday life. It can also lower your risk of cardiovascular disease and help you sleep better at night. The best way to achieve relaxation is through a combination of physical and mental techniques, such as mindfulness, visualization, and progressive muscle relaxation.
Often, you will be asked to complete a form or questionnaire upon entering a spa to ensure that they can provide you with a safe and enjoyable experience. You can then choose from a range of facilities, such as a gym or fitness suite and thermal suites. Many resort spas will also have saunas, steam rooms, and hot tubs. You can also hire robes and slippers for your visit, although it is usually recommended that you bring your own so you don’t catch an infection.
Detoxification
While the word “detox” has been co-opted to become a health fad, in its original sense it refers to a medical procedure that rids the body of dangerous, sometimes life-threatening, levels of alcohol or drugs. Medical detoxification is typically done under the supervision of a doctor and involves a regimented course of medication and other therapies.
Detoxification products and treatments claim to cleanse the body by flushing out perceived toxins through the skin, colon and other organs. While it’s true that our bodies are naturally designed as detoxification machines, they can be tripped up by foods high in sugar, fat and caffeine or weighed down by excess fluids. As a result, many people are looking for ways to improve their health through detoxification.
Unfortunately, most of the products and diets that are sold as detoxification aids aren’t backed up by research and can cause significant harm to health. For example, juices used in detoxification diets often aren’t pasteurized and can contain harmful bacteria that cause diarrhea and other serious illnesses. Moreover, detox diets that are very restrictive can make it difficult to meet nutritional needs and may lead to malnutrition.
On the other hand, a detox spa treatment that helps to reduce bloating and fluid retention while enhancing circulation and lymphatic drainage can help support the body’s natural ability to eliminate toxins. This can boost energy levels, reduce stress and contribute to a sense of wellbeing.
A detox spa treatment that includes massage therapy can be particularly effective, especially if the massage technique incorporates manual lymphatic drainage techniques. This technique stimulates the lymphatic system to help eliminate toxins and waste, which is also beneficial for the skin.
In addition, many spa body treatments, such as mud and seaweed wraps, can enhance the skin’s natural ability to expel toxins. These treatments also can improve circulation, rejuvenate the skin and reduce stress. Finally, a detox treatment that involves a sauna or steam room can provide even more benefits by helping the body sweat out toxic substances. This can be a great way to start the new year off with a healthy glow.
Happiness
Happiness is an electrifying and elusive state that’s been a focus of longing among philosophers, theologians, psychologists and economists. Since the 1990s, a whole branch of psychology-positive psychology-has been devoted to pinning it down, and recent research suggests that happiness is a longer-term condition that may stem from healthy habits and lifestyle choices.
Happier people tend to achieve more, have better relationships and a greater sense of fulfillment in their lives. They’re also more resilient against stress, depression and anxiety, and they have a greater appreciation of the beauty of life. Happiness has even been linked to a healthier body and a longer lifespan.
Theories of happiness vary widely, but hedonists typically emphasize feelings of pleasure and well-being that stem from enjoyable experiences. Other theories, known as eudaimonic or meaning-focused happiness, focus more on fulfilling responsibilities and pursuing goals that promote virtue. A third possibility, called hedonic or emotional-state happiness, focuses on the experience of positive emotions such as joy and contentment.
In the scientific literature, there are two basic approaches to defining happiness. One, called subjective well-being, combines three broad categories of affective states: endorsement states like joy and serenity, engagement states such as flow and a sense of vitality and attunement states like tranquility and confidence. Another, based on the work of Martin Seligman and Ed Diener, defines happiness as an overall sense of fulfillment that relates to life’s meaning and purpose.
While a number of different factors contribute to happiness, it’s been shown that you can increase your own level of happiness by practicing gratitude, connecting with nature and spending time with friends and family. A growing body of evidence shows that these activities can improve your cardiovascular health, immune system and inflammation levels, and lead to a more balanced life.
While it’s possible to sift through the various claims and controversies surrounding happiness, most philosophers agree that it is a valuable goal for people of all backgrounds to pursue. Some critics object that narrower theories of happiness, such as those focused on hedonic or emotional states, fail to take important concerns into account. However, these objections often misunderstand the distinction between a hedonistic view of happiness and an ethical account of it.
Health
Taking time to relax and recharge with spa treatments can boost your mental health and improve your quality of life. It can also reduce stress and help you sleep better, which leads to more energy. The practice of spa therapy can also promote spiritual healing, which can be beneficial for both physical and emotional health.
The calming effect of warm water and rhythmic jets relaxes muscles and eases tension. A hot tub is also great for reducing joint pain, especially when used in conjunction with massage. Many spas also offer guided meditation or mindfulness practices, which can help you focus on the present moment and reduce anxiety.
Spas are not just about relaxation and detoxification, they can actually help with a number of common health problems. Depending on the type of spa, you can boost your immune system with a subzero cryotherapy chamber, soothe sore muscles with a mud bath, or get a body scrub down to your last hair follicle with a red wine ‘vinotherapy’ treatment.
Stress is a common problem in modern society and can be damaging to your mental and physical health. Studies show that chronic psychological stress can lead to a loss of ability to regulate the immune system and increase your risk for disease, including cardiovascular disease, metabolic disorders, and infectious diseases. Spa treatments like massage and aromatherapy are known to relieve stress and increase self-esteem, which can lead to better mental and physical health.
A massage can leave your muscles feeling relaxed and loose, which in turn reduces inflammation in the joints and other parts of the body. It also increases blood flow, which in turn reduces pain and helps prevent muscle fatigue. It also decreases heart rate and blood pressure, which can lower your risk of high blood pressure and diabetes.
It is important to note that spa treatments that involve breaks in the skin can be a risk for germ transmission, particularly if you have a condition such as dermatitis or psoriasis. If you have a condition that can be compromised by germs, it is best to avoid full-body exfoliation and use a robe and slippers for your visits.